3D Laser Cutting Machine
Product Description
The sheet metal covering parts of auto parts include engine cover, rear cover box, water tank frame, bumper, fender, door, and ingot beam of chassis parts, control arm, rear axle, etc., which often require three-dimensional cutting, including Trimming and punching, etc., traditional processes include mold punching, plasma cutting or laser cutting on five-axis machine tools.
Using the die-opening stamping process, the trimming and punching processes have always been difficult in the mold making process, especially for some large automobile molds with complex structures. The determination of the trimming line needs to be repeatedly explored several times or even more than ten times, which brings a huge workload to the fitter and processing equipment, and not only puts forward higher requirements on the skill level of the fitter. In addition, in the small batch or prefabrication stage, the cost of developing molds is high, the cycle is long, and the change is not flexible.
The use of plasma cutting results in irregular cut edges, which require polishing in the next process, which is time-consuming and labor-intensive. Small holes can only be processed with a hand drill or a punch, which is inefficient. Moreover, the handheld ion device has certain radiation to the human body, and the dust seriously pollutes human health.
The specific process flow is as follows:
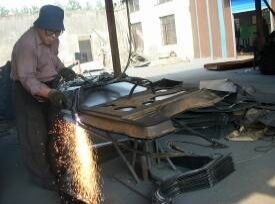
Handheld plasma equipment edge cutting process
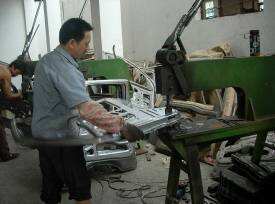
Manual punching process
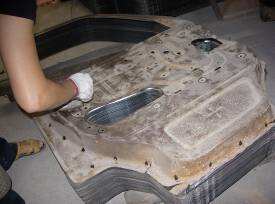
Marking and positioning before punching
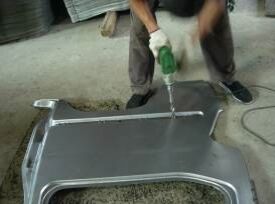
Hand drill hole punching
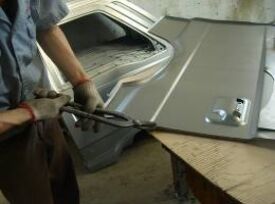
Trimming after plasma cutting
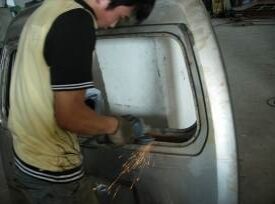
Sanding after plasma cutting
Some large-scale manufacturers took the lead in introducing advanced five-axis laser cutting machines, which greatly improved the process effect and However, the five-axis machine tool covers an area of up to tens of square meters and is extremely expensive. It is a product that is difficult to popularize for the majority of small and medium-sized manufacturers.
New Process Enabled Using Industrial Robots and Fiber Laser Equipment
According to a large number of market research in the early stage, combined with the industry characteristics of automobile sheet metal cover parts and chassis parts, our company now introduces the combination of industrial robot + fiber laser for three-dimensional cutting, which can effectively meet the needs of automobile manufacturing, aerospace, marine engineering and other industries. .
First, replace the five-axis machine tool with an industrial robot. Both can describe the spatial trajectory to achieve three-dimensional cutting. repetitive positioning accuracy of industrial robots is slightly lower than that of five-axis machine tools, about ±100um, but this can fully meet the accuracy requirements of the automotive sheet metal cover and chassis parts industry. . The use of industrial robots greatly reduces the cost of the system, reduces power consumption system costs and system operation and maintenance costs. and reduces the system footprint.
Specifications
Second, the main equipment configuration list:
Serial number | Project Name | Specification Model | Quantity | Origin | Remarks |
1 | Fiber Laser | RAYCUS -3000W | One set | RAYCUS/MAX | With three-dimensional armor |
2 | Fiber laser special 3D cutting head | One set | RAYTOOLS | Key components imported from Germany, including anti-collision system | |
3 | Z-axis servo lift mechanism | Stroke 60mm | One set | Japan Panasonic servo with holding brake, high precision | |
4 | Elevator control | One set | FRIENDNESS | Highly tracked | |
5 | PWM 3D cutting control software and HMI screen | One set | Thick plate cutting and small circle cutting laser light output mode, power control | ||
5 | TCP auto-calibration | One set | |||
6 | Power Control Module | One set | Fanuc Japan | ||
7 | Software packages | One set | Fanuc Japan | ||
8 | Water cooling system for fiber laser | HL-3000 | One set | HANLI | Dedicated fiber laser cooling system |
9 | Three-dimensional robot | FANUC-M20IA/20 | One set | FANUC | 3-D programming, 20KGload |
11 | Gantry | One set | Provide drawings, demand-side production, or supply-side provision | ||
13 | Cutting special control system and electric control cabinet | HLCF-18D-FR-3000 | One set | Standard | |
14 | Installation, commissioning, inspection | HLCF-18D | Once | ||
15 | Technical Services and Training | HLCF-18D | One set | ||
16 | Spare parts | HLCF-18D-FR-3000 | One set | See random attachment |
In order for the laser cutting machine to work stably for a long period of 24 hours, there are requirements for water, electricity, gas, working environment, foundation, processing materials, etc. as follows:
1 | Power supply | Lasers | 8KVA | The total installed capacity is not greater than20KVA. |
Water Chillers | 3KVA | |||
Robotics | 4KVA | |||
Other accessories | 1KVA | |||
Three-phase five-wire system | 380V±5%, 50Hz | |||
Three-phase power imbalance | Less than 2.5% | |||
Grounding | Less than 4 ohms | |||
2 | Water | Cooling water for chillers | Distilled water | |
3 | Gases | Cutting gas | O2>99.95% | Different processing parameters for different materials |
4 | Jobs Environment |
Temperature requirements | 5 - 40 degrees | Lasers need to be installed in air-conditioned rooms |
Humidity requirements | Less than 70% | |||
Foundation requirements | There must be no obvious source of earthquake nearby | Foundations with obvious earthquake sources need to be seismic trenches | ||
5 | Plate | No rust and corrosion on the surface |
-
Automated Laser Welding System
-
Automated Laser Welding System
-
Automated Laser Welding System
Quick Detail
Main technical specifications of the machine.
1、Processing width (L×W×H).
FANUC-M20IA: 2200mm × 1800mm × 200mm (specific cutting width and the shape and height of the workpiece)
2、Robot effective radius and load:FANUC/ 1811mm
3、Repeat positioning accuracy of robot: FANUC: ±0.05mm
4 、Robot path accuracy:FANUC: ±0.15mm
5 、Maximum table load:20kg (at the center of the flange)
6, Power supply: three-phase five-wire AC380 (±10%) V, frequency: 50HZ
7 、Total power protection level:IP54
8 、Main processing parts: (depending on customer product shape and process requirements)
9、 Processing plate thickness: the limit thickness of carbon steel plate ﹤6mm (5mm aluminum plate), cutting situation refer to the following diagram
Competitive Advantage
Precision: Robotic 3D laser cutting provides exceptional precision and accuracy. This precision ensures high-quality and consistent results, even for intricate shapes and patterns. patterns.
Versatility: Robotic 3D laser cutting is highly versatile and can cut a wide range of materials, including metals (such as steel, aluminum, and copper), plastics, composites, and more. The laser beam can adapt to various material thicknesses and properties, making it suitable for diverse applications across industries
Speed and Efficiency: Robotic 3D laser cutting is a fast and efficient cutting method. The robot can move quickly and precisely along complex paths. The high cutting speed and automated nature of robotic systems contribute to increased productivity and throughput. The high cutting speed and automated nature of robotic systems contribute to increased productivity and throughput.
Complex Geometries: Robotic 3D laser cutting excels at cutting complex shapes and geometries. The flexibility of the robotic arm enables access to hard-to-reach areas, allowing for intricate cuts and contours that may be challenging or impossible with traditional cutting methods. This capability is particularly beneficial in industries such as automotive, aerospace, and architecture.
Minimal Material Distortion: Laser cutting produces a narrow and focused heat-affected zone, minimizing thermal distortion on the material being cut. This results in cleaner edges, reduced warping, and less post-processing requirements, ultimately improving the overall quality of the cut parts This results in cleaner edges, reduced warping, and less post-processing requirements, ultimately improving the overall quality of the cut parts and reducing the need for additional finishing steps.
Automation and Integration: Robotic 3D laser cutting can be integrated into automated production lines and workflows, streamlining the The robotic system can be programmed to perform a series of cutting tasks autonomously, reducing the need for manual The robotic system can be programmed to perform a series of cutting tasks autonomously, reducing the need for manual intervention and increasing overall production efficiency.
Safety: Laser cutting offers enhanced safety compared to traditional cutting methods. The cutting process is contactless, minimizing the risk of Additionally, modern robotic laser cutting systems incorporate safety features such as protective enclosures, interlock systems, and sensors to ensure safe operation and protect operators from laser radiation. In addition, modern robotic laser cutting systems incorporate safety features such as protective enclosures, interlock systems, and sensors to ensure safe operation and protect operators from laser radiation.